cGMP Guideline for Packing Material in pharmaceuticals is explain in this article.
cGMP Guideline for Packing Material
1. Materials examination and usage criteria
(a) Written procedures describing in detail the receipt, identification, storage, handling, sampling, examination, and/or testing of labeling and packaging materials must be developed, approved, and followed. These materials must be representatively sampled, examined, or tested on receipt and accepted by the quality control unit before use as per cGMP Guideline for Packing Material.
(b) Any materials that do not fully meet acceptance criteria must be rejected to prevent their use.
(c) Records of each receival of each different label and packaging material must be maintained indicating receipt, examination or testing, and whether accepted or rejected.
(d) Labels and other labeling materials for each different drug product, strength, dosage form, or quantity of contents must be stored separately with suitable identification. Access to the storage area must be limited to authorized personnel.
(e) Obsolete and outdated labels, labeling, and other packaging materials must be quarantined and destroyed.
(f) The use of gang – printed labels for different drug products or different strengths or different net contents is prohibited. The only exception to this rule is if labels from gang – printed sheets are adequately differentiated by size, shape, or color that will prevent mixing of labels as per cGMP Guideline for Packing Material.
(g) If cut labeling is used, packaging and labeling operations must include one or more of the following special control procedures:
(i) Dedication of a labeling and packaging line to each different strength of each different drug product as per cGMP Guideline for Packing Material.
(ii) Use of appropriate electronic or electromechanical equipment to conduct a 100% examination as per cGMP Guideline for Packing Material.
(iii) Use of visual inspection to conduct a 100% examination for correct labeling. If visual inspection is used, the inspection should be performed by one person and independently verified by a second individual.
(h) Printing devices on or associated with the manufacturing line must be monitored to assure that the printing conforms to the print specified in the batch production record.
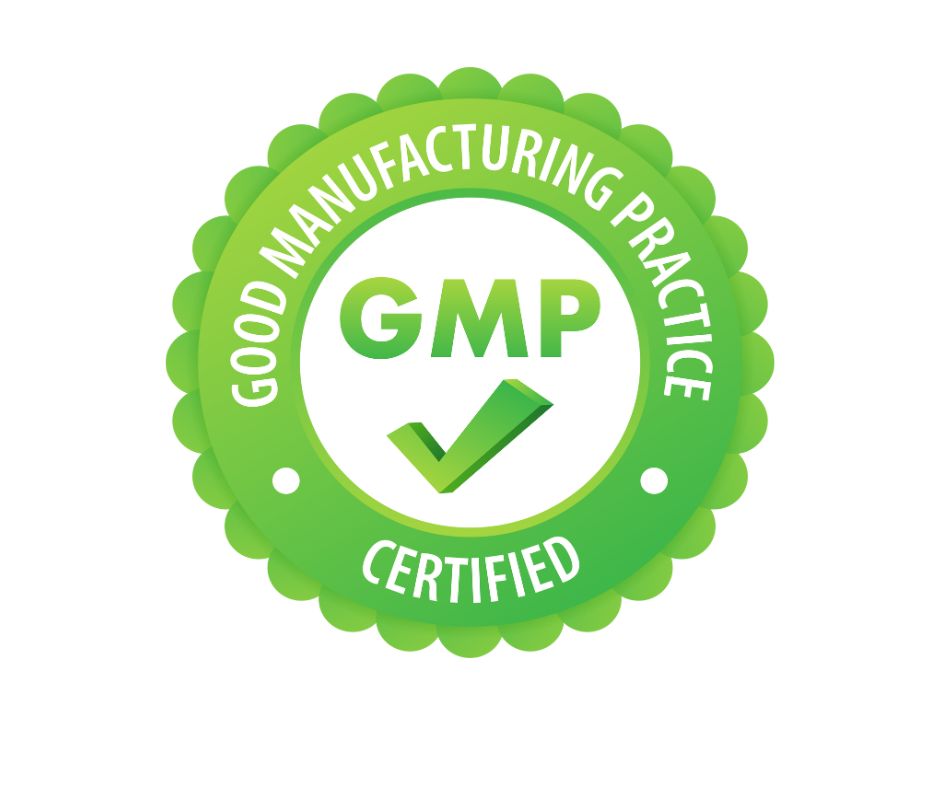
2. Issuance of labeling
(a) Strict control should be exercised over the issuance of labeling.
(b) Labeling materials issued for a batch must be carefully examined for identity and conformity to the labeling specified in the batch manufacturing record as per cGMP Guideline for Packing Material.
(e) All excess labeling bearing a lot or control number must be destroyed.
(f) Returned labeling should be maintained and stored in a manner to prevent mix – ups.
3.1 There must be written procedures designed to assure that correct labels, labeling, and packaging materials are used. These procedures should incorporate the following features:
(a) Prevention of mix – ups and cross – contamination by physical or spatial separation of operations on other drug products.
(b) Identification and handling of filled drug product containers that are set aside and held in unlabeled condition for future labeling operations. Such procedures should be designed to prevent mislabeling individual containers, lots, or portions of lots. It is not necessary to apply identification to each individual container, but the procedure should be adequate to determine the name, strength, quantity of contents, and lot or control number of each container.
(c) Identification of the drug product with a lot or control number that permits determination of the history of the manufacture and control of the batch.
(d) Examination of packaging and labeling materials for suitability and correctness before issuing for use and before packaging operations. These examinations must be documented in the batch production record.
(e) Inspection of the packaging and labeling facility immediately before use to assure that all drug products and labeling materials from the previous operation have been removed. Inspection results must be documented in the batch Manufacturing record.
3.2 Tamper – evident packaging requirements for OTC human drug products
Drug product inspection
(a) Packaged and labeled products must be examined during finishing operations to provide assurance that containers and packages in the lot have the correct label.
(b) A representative sample of units should be collected at the completion of finishing operations and should be visually examined for correct labeling.
(c) Results of these examinations must be recorded in the batch production records. Expiration dating
(a) All packaged drug products must carry an expiration date that has been determined from appropriate stability testing.
(b) Expiration dates must be related to the recommended storage conditions stated on the label as determined by stability studies.
(c) If the drug product is to be reconstituted at the time of dispensing, its label must carry expiration information for both the reconstituted and unreconstituted forms.
(d) Homeopathic drug products are exempt from the requirements of this section.
(e) Allergenic extracts that are labeled “ No U.S. Standard of Potency ” are exempt.
(f) New drug products for investigational use are exempt provided that they meet appropriate standards or specifications as demonstrated by stability studies during their use in clinical investigations. If new drug products for investigational use are to be reconstituted at the time of dispensing, their labeling must bear expiration information for the reconstituted product.
3. Warehousing procedures
(a) Written procedures describing the warehousing of drug products must be written and followed. These procedures should include:
(i) Quarantine of drug products before release by the quality control unit.
(ii) Storage of drug products under appropriate conditions of temperature, humidity, and light so that the quality of the drug products is not affected.
(iii) Distribution procedures
(a) A procedure that assures the distribution of the oldest approved stock first. Deviation from this procedure is acceptable if it is temporary and appropriate.
(b) A system for documenting distribution so that distribution of each lot of drug product can be readily determined to facilitate its recall if required.