Current Good Manufacturing Practice, a set of regulations that ensure the quality, purity, and consistency of pharmaceutical products and other regulated goods. It’s a key aspect of quality assurance, ensuring products are consistently manufactured and controlled to meet the required quality standards.
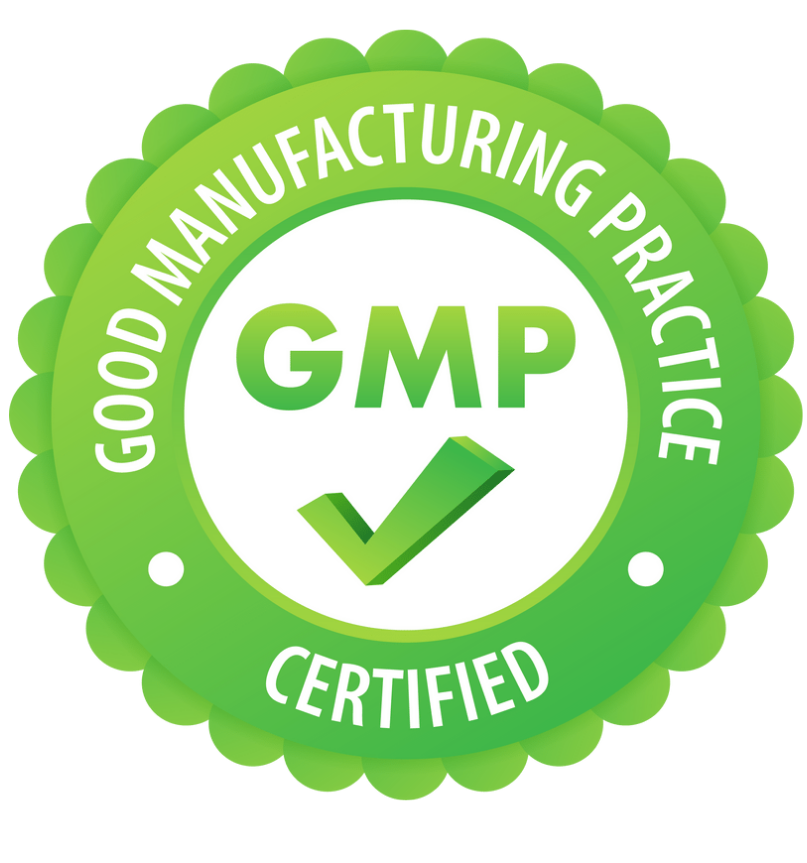
Current Good Manufacturing Practice
This guidance document was written by the FDA to help manufacturers implement what they consider to be modern quality systems and risk management approaches that will meet the requirements of the FDA ’s GMP regulations. The guidance describes what the FDA considers a comprehensive quality systems (QS) model. It also explains how manufacturers can be in full compliance with the Current Good Manufacturing Practice (GMP) regulations by implementing such quality systems. The FDA does not intend this guidance to place new expectations on manufacturers nor does this replace the GMPs. As is true with all guidance documents, this document does not establish legally enforceable responsibilities, but rather it describes the FDA ’ s current thinking. Thus, this guidance should be viewed as a set of recommendations unless a regulation is cited. The objective of this guidance is to describe a quality systems model and demonstrate how and where the elements of this model can fit within the requirements of the Current Good Manufacturing Practice (cGMP) regulations. The philosophy being put forward is that quality should be build into the product, and testing alone cannot be relied on to ensure product quality.
CGMPS and the Concepts of Modern Quality Systems
The FDA believes that several key concepts are critical for any discussion of modern quality systems. The following concepts are used throughout this guidance as they relate to the manufacture of pharmaceutical dosage forms:
Quality:
For the purposes of this guidance, the phrase achieving quality means achieving the identity, strength, purity, and other quality characteristics designed to ensure safety and effectiveness. Quality by Design and Product Development.
This means designing and developing a product and its associated manufacturing processes that will be used to ensure that the product consistently attains a predefined quality at the end of the manufacturing process.
This component of a quality systems framework can help guide the setting of specifications and process parameters for dosage form manufacturing, assess and mitigate the risk of changing a process or specification, and determine the extent of discrepancy investigations and corrective actions.
Corrective and Preventative Action (CAPA).
This is a regulatory concept that focuses on investigating, understanding, and correcting discrepancies while attempting to prevent their recurrence.
This model separates CAPA into three separate concepts:
- Remedial corrections of an identified problem
- Root cause analysis with corrective action to help understand the cause of the deviation and prevent recurrence of a similar problem
- Preventative action to prevent recurrence of similar problems
Change Control
This process focuses on managing change to prevent unintended consequences.
Quality Unit
While the Current Good Manufacturing Practice (cGMP) refer to a quality unit, current industry practice is to divide the responsibilities of this unit between two groups:
• Quality control (QC) usually involves
(a) assessing the suitability of incoming components and the finished products
(b) evaluating the performance of the manufacturing process
(c) determining the acceptability of each batch for release and distribution
• Quality assurance (QA) involves
(a) review and approval of all procedures related to manufacturing and maintenance
(b) review of records
(c) auditing and performing/evaluating trend analyses.
Six – System Inspection Model
The FDA ’s instruction manual for its investigators is a systems – based approach to inspection consistent with this guidance.
The FDA defines six interlocked systems:
(1) the quality system which encompasses all the other systems
(2) a materials system
(3) a production system
(4) a packaging and labeling system
(5) a facilities and equipment system
(6) a laboratory controls system. The agency believes that use of this overall system approach will help firms achieve better control.
Quality Systems Model
This section was written to describe a model for use in pharmaceutical manufacturing that can supply the controls to consistently produce a product of acceptable quality. The model is described by four major factors:
- Management responsibilities
- Resources
- Manufacturing operations
- Evaluation
Management Responsibilities
The FDA feels that a robust quality system model calls for management to play a key role in the design, implementation, and management of the quality system.
Resources
Sufficient resources should be provided to create a robust quality system that complies with the Current Good Manufacturing Practice (cGMP) regulations. Senior management or a designee should be responsible for providing adequate resources.
Facilities and Equipment
The technical experts who have an understanding of pharmaceutical science, risk factors, and manufacturing processes related to the product are responsible for defining specific facility and equipment requirements. The equipment must be qualified, calibrated, cleaned, and maintained to prevent contamination and product mix – ups. It is important to remember that the Current Good Manufacturing Practice (cGMP) place as much emphasis on process equipment as on testing equipment while most quality systems focus only on testing equipment.
Control Outsourced Operations
Quality systems call for contracts with outside suppliers that clearly describe the materials or service, quality specification responsibilities, and communication mechanisms.
Manufacturing
There is an overlap between the elements of a quality system and the GMP regulation requirements for manufacturing operations. One should always remember that the FDA ’s enforcement programs and inspectional coverage are based on the GMPs. The FDA feels that the following factors are essential in a manufacturing quality system:
- Design, develop, and document product and processes
- Examine inputs
- Perform and monitor operations
- Address nonconformities
Evaluation Activities
This includes the following activities:
- Analyze data for trends
- Conduct internal audits
- Quality risk management
- Corrective action
- Preventative action
- Promote improvements